Metal Stamping: Secret Considerations for Quality and Performance
Metal Stamping: Secret Considerations for Quality and Performance
Blog Article
Metal Marking Advancements: Elevating Production Processes for Superior Outcomes
In the world of manufacturing procedures, metal marking has long been a keystone technique for generating a selection of accuracy components. Nonetheless, with the unrelenting march of technological improvement, the landscape of steel marking is undergoing a significant makeover. Advancements in this field are not only improving the performance and high quality of production yet are additionally paving the method for new possibilities that were previously past reach. As the sector welcomes these innovative advancements, a redefinition of what is possible in production is underway, appealing exceptional results and setting new requirements for excellence in the field.
Advancement of Steel Stamping Strategies
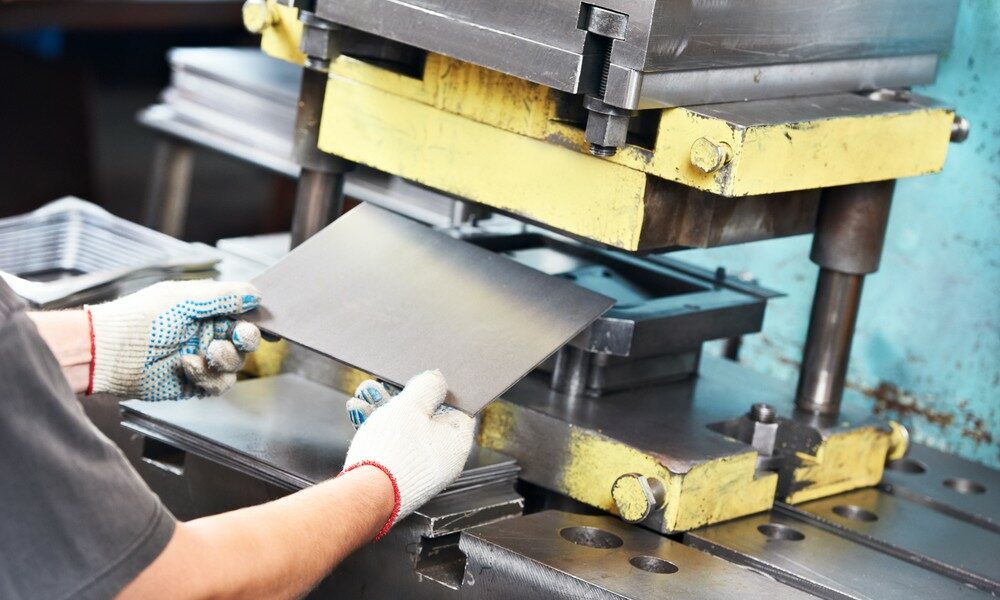
Additionally, developments in product science have actually caused the development of high-strength alloys that can currently be perfectly marked into complex forms, accommodating a wider array of commercial applications. The integration of robotics and expert system has better enhanced the marking procedure by enhancing rate and accuracy while lowering the threat of human mistake.

Effect of Advanced Materials
Have innovative materials changed steel marking procedures dramatically in the production sector? By making use of products such as high-strength alloys, progressed composites, and innovative finishings, steel marking processes can now produce parts that are lighter, more powerful, and a lot more sturdy than ever previously.
These innovative products offer superior mechanical buildings, rust resistance, and thermal security, enabling producers to meet the needs of modern-day sectors such as aerospace, automotive, and electronics. Furthermore, making use of advanced products in metal marking has helped with the production of complicated geometries and intricate styles that were previously unattainable via traditional methods.
Additionally, the execution of sophisticated products has caused minimized product waste, reduced manufacturing expenses, and shorter lead times, making steel marking procedures extra sustainable and economical. As modern technology continues to advancement, the effect of sophisticated materials on steel marking processes is anticipated to drive additional technology and boost the competition of suppliers in the international market.
Automation in Steel Stamping
The advancement of steel marking procedures driven by the integration of innovative products has set the phase for considerable innovations in automation within the manufacturing market. Automation in metal stamping has actually revolutionized production processes, improving effectiveness, accuracy, and general output top quality. Through the use of robotics, sensing units, and computer-controlled systems, jobs that were once manual and time-consuming can now be performed with unrivaled speed and accuracy.
Automation in steel marking not only increases production prices but likewise makes sure uniformity in the production procedure. By lessening human intervention, the danger of errors is significantly minimized, leading to greater levels of product harmony and dependability. In addition, automation enables suppliers to carry out complex click marking tasks that would certainly be tough or not practical to achieve manually.
Moreover, automation in steel stamping adds to a safer working setting by lowering the need for employees to participate in unsafe or repetitive tasks - Metal Stamping. This change in the direction of automation not only enhances productivity but likewise leads the way for the future of production, where modern technology plays a central role in driving functional quality
High Quality Control and Examination Systems
With a concentrate on precision and dependability, top quality control and inspection systems play a crucial function in guaranteeing item excellence in metal marking procedures. These systems are developed to check every stage of production, from material examination to the end product, to guarantee that all parts satisfy the called for standards. By executing sophisticated innovations such as optical inspection systems, coordinate measuring makers (CMM), and automated assessing tools, makers can identify also the tiniest variances in measurements, surface quality, and total honesty of stamped parts.
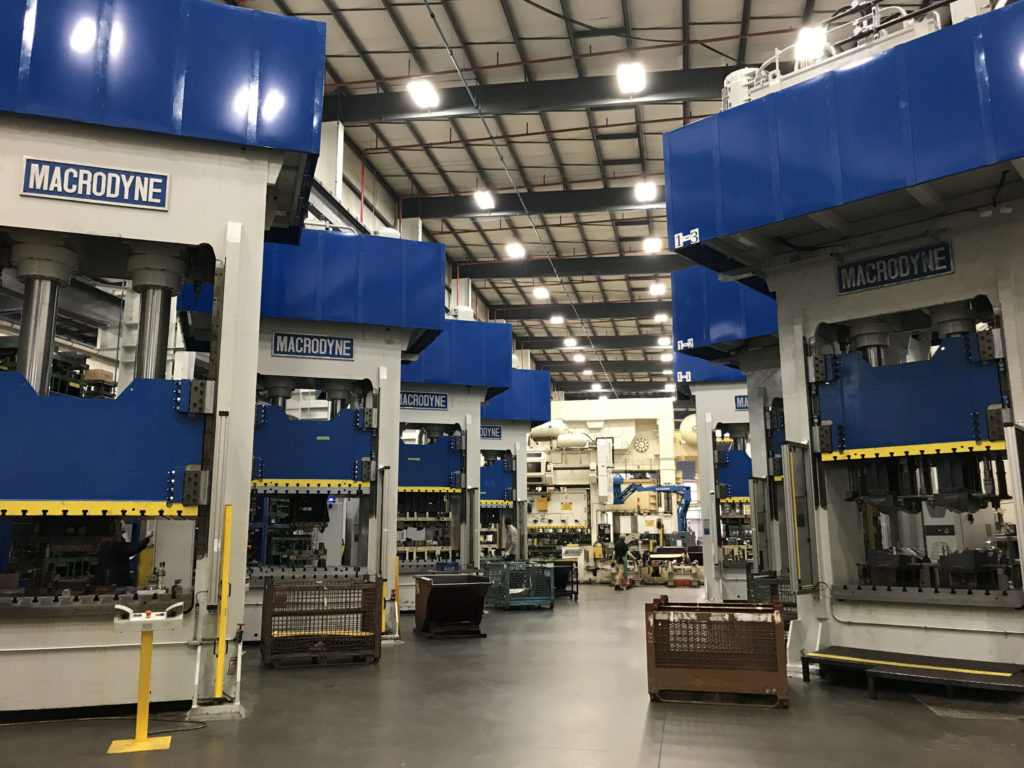
Sustainability Practices in Steel Stamping
Structure upon the structure of accuracy and reliability developed via high quality control and examination systems, the combination of sustainable practices in steel marking procedures is progressively becoming a centerpiece for suppliers seeking to lessen ecological influence and maximize resource application. Sustainability practices in steel marking encompass a variety of campaigns aimed at decreasing waste generation, power intake, and greenhouse gas discharges throughout the manufacturing procedure.
One secret element of sustainability in metal marking is the fostering of environmentally friendly materials and technologies that promote recyclability and waste decrease. By using recycled products and applying energy-efficient machinery, manufacturers can reduce their carbon impact and add to a more lasting production cycle. Furthermore, optimizing manufacturing processes to decrease product waste and energy use not just benefits the environment yet likewise causes set you back financial savings for organizations Extra resources in the long run.
Moreover, the execution of lasting methods in steel stamping can improve brand name track record and attract environmentally conscious consumers. As sustainability continues to gain value in the production market, integrating environmentally friendly initiatives into metal marking processes is vital for long-term success and competitiveness in the marketplace.
Verdict
Finally, steel marking strategies have informative post dramatically developed with time, incorporating sophisticated products and automation to enhance making processes. Quality control and assessment systems play a crucial role in making sure premium results, while sustainability practices are progressively being carried out to lower environmental effect. These technologies in metal marking have actually revolutionized the market, bring about much more effective and lasting manufacturing methods for numerous sectors.
Metal marking, when a handbook and labor-intensive procedure, has changed into an extremely automated and sophisticated method of shaping steel sheets right into numerous kinds and layouts.Have innovative products changed steel marking processes dramatically in the production market? By using materials such as high-strength alloys, advanced composites, and innovative coverings, metal stamping processes can now generate parts that are lighter, more powerful, and a lot more sturdy than ever in the past.
The evolution of metal stamping procedures driven by the assimilation of advanced materials has actually established the stage for considerable innovations in automation within the manufacturing market.In verdict, metal marking techniques have actually significantly evolved over time, integrating advanced materials and automation to enhance producing processes.
Report this page